锂离子电池对隔膜材料的要求
导读:隔膜是锂离子电池的重要材料,它体现两种重要的功能:一是保证电池安全;二是使电池与充放电相关的功能得以实现。电池能量密度的提升,主要基于电极材料体系的发展和优化;而电池的容量发挥、倍率性能、循环寿命、充电电位、首次库仑效率、自放电、高低温特性、内短路和析锂等重要特性,都与隔膜材料的特性和品质相关。
隔膜根本的作用就是隔离正极片和负极片,避免短路。同时,基于锂离子电池的工作机制:充电时锂离子从正极材料中脱出、穿过隔膜迁移插入到负极材料的层状结构间;放电时锂离子从负极材料脱出、反向穿过隔膜重新迁移嵌入正极材料中(图1)。
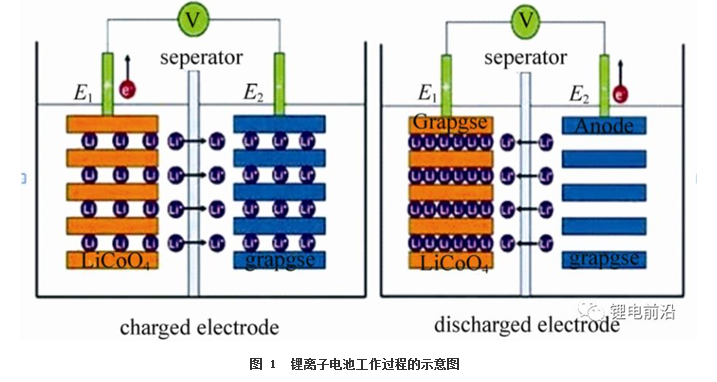
因此,隔膜上需要有贯通的微孔供锂离子迁移;对于隔膜而言最重要的特性就是微孔结构。锂电隔膜微孔结构量化的技术参数主要包括:孔径、孔径分布、孔隙率;不易量化的结构特征还有在拉伸过程中成纤的程度、成孔的均匀性、盲孔和闭孔的比例等。一种隔膜的微孔结构可以清楚的反映其生产工艺的特点及设备水平,也反微孔结构最便捷的方法是扫描电镜(SEM)。采用SEM可以直观映出生产企业为提高隔膜品质而遇到的各种困难。表征一种隔膜表面地看到隔膜的均匀性、表面微孔的形状、尺寸及大致分布情况。更准确的信息需要通过压汞仪、毛细管流动分析仪来获得。
目前商品化的锂电隔膜主要有两类:一种是用机械拉伸造孔工艺制造的聚烯烃隔膜(PP、PE、PP/PE/PP);另一类是无纺布/陶瓷颗粒复合隔膜。为增强聚烯烃隔膜的安全性而发展的陶瓷涂布(或其它类型的涂布),是对第一类隔膜性能的补足。高比能、高功率动力电池的研究和工业化给隔膜的发展提出了很高的要求,高安全性、耐高电压的优质隔膜一直是锂电材料研究领域的热点。但是,目前还没有新型隔膜真正进入工业化制造阶段。
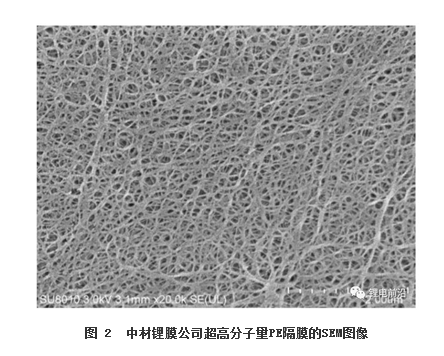
全球范围内,锂电隔膜的主要市场集中在日本、中国、韩国和美国;而领先的生产技术基本掌握在日本和美国的少数企业手中。但随着2015年旭化成收购Celgard,日本成为锂电隔膜制造业的领跑者。我国2016年隔膜需求量约为20亿m2,产量12亿m2左右,进口比例约占40%;而高端动力电池隔膜的进口率更高,达70%。2017年全球隔膜产量估算在23.8亿m2左右,同比增长25.3%,其中干法隔膜占比42%,湿法隔膜占比58%,全球锂电池隔膜增速较快,由于下游需求的增长,预计全球市场规模将保持20%以上的增长。
2017年4月工信部等三部委发布《关于印发< 汽车产业中长期发展规划>的通知》指出:“2020年,新能源汽车年产销达到200万辆......到2025年,新能源汽车占汽车产销20%以上。” China EV100《锂和电池企业可持续发展研究报告 2017》中引用 2020—2025年中国动力锂电池市场需求预测中的数据,2020年200万辆、2030年1520万辆新能源汽车,分别需要130GW·h 和500GW·h动力电池。相应地,可以计算出所需的高品质动力电池用隔膜的需求量大致是2020年20亿m2、2030年90亿m2/年。如果加上储能用电池和消费电子类电池对隔膜的需求,上述计算的隔膜需求大致将会是2020年30亿m2和2030年100亿m2。
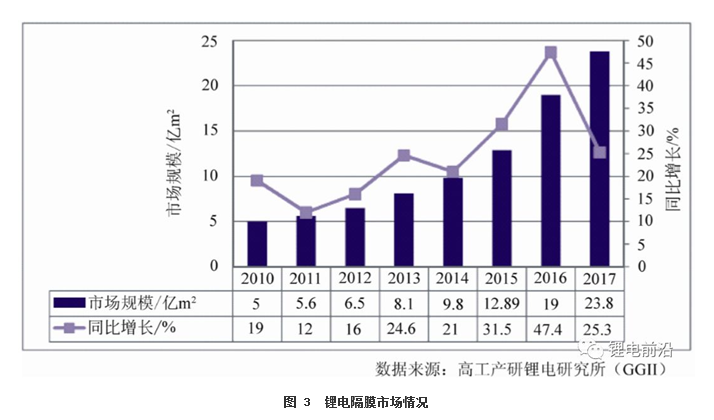
国内锂电隔膜相关标准的现状
不同膜企的生产工艺和设备不同,而隔膜产品的特性与工艺和设备的相关性极高,所以在行业内制定隔膜产品的标准作用不大。而有意义的是企业制定自己的产品标准,规范生产工艺、确保产品质量的一致性。目前能够检索到的主要是一些隔膜的检测标准,见表1。我国十几年来颁布的隔膜材料相关标准,其中国家标准14项、国家质量检测标准1项、行业标准1项。从类别上看,产品标准1项,测试和分析方法15项。绝大部分是中国国家标准化管理委员会组织起草、审核、发布的。相对制造和产品的标准而言,隔膜的检测标准相对容易制定并被业内接受,在实际的检测工作中已逐渐被参考或应用。
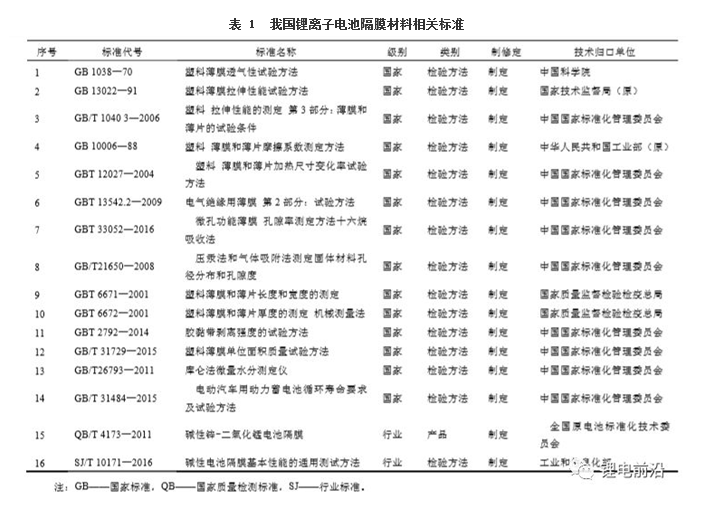
锂离子电池对隔膜材料的要求
隔膜的性能影响电池极片与隔膜的界面、电解质的保持、锂离子的传导、电池内阻、充放电性能、循环寿命、安全性能等。通常,对隔膜的性能有如下要求。
①均匀性,包括厚度均匀、张力均匀、微孔分布的均匀性等;
② 一致性,指产品质量的批次一致性;
③在保证安全的前提下,降低隔膜厚度,提高电池的能量密度/功率密度;
④提高孔隙率到合理范围,改善电池的倍率性能;
⑤优化的孔径分布;
⑥提高耐热性,保证电池异常发热时隔膜不发生大比例收缩;
⑦有足够的机械强度和断裂拉伸比例,保证在外力作用时的可靠性;
⑧提高耐氧化性,保证电池寿命以及对高电压工况的适用性;
⑨提供可以对电池形成有效保护的闭孔温度;
⑩化学/电化学稳定性;耐击穿电压高;含水量低(降低电解液分解,提高电池的成品率)。
在隔膜的原材料选择、生产、运输、销售的各个环节,都会因人、机、料、法、环、测等条件因素的变化而发生波动。因此,从原材料的筛选到最终的销售均需依据标准进行操作,并按标准进行检验,以确保产品的实用性、一致性和可靠性。用户关心的是产品的功能、一致性和可靠性,产品质量的控制主要检测以下技术指标。
隔膜的厚度
厚度是考虑电池综合性能和安全性能而确定的。厚度均匀性是生产过程中需要严加控制的质量指标之一,厚度偏差是由当前隔膜行业水平和电池装配能够接受的程度确定的。隔膜越薄,溶剂化锂离子穿越时遇到的阻力越小,离子传导性越好,阻抗越低,但隔膜太薄时,其保液能力和电子绝缘性降低,也会对电池性能带来不利的影响。对于消费类锂离子电池(手机、笔记本电脑、数码相机中使用的电池),随着使用的日益增长,更薄的隔膜,比如7μm,甚至更薄的隔膜开始大范围的应用。将聚烯烃类隔膜往更薄的方向发展,以满足3C锂离子电池的性能需求,是以后提升电池性能的一大关键切入点。对于动力电池来说,由于装配过程的机械要求,往往需要更厚的隔膜,当然对于动力用大电池,安全性也是非常重要的,而厚一些的隔膜往往同时意味着更好的安全性,EV/HEV使用的是总厚度为16~25μm的隔膜。一般来说隔膜的厚度越厚,其机械强度越高,能在一定程度上保障电池的安全性,但对于穿刺性破坏、电池结构破坏和超高温冲击起到作用较小,电池最终的安全性还需要改善正负极材料和电解液的稳定性来保障。目前隔膜厂家对厚度测量一般参照《GB/T 6672—2001塑料薄膜和薄片厚度测定机械测量法》或 ISO4591:1992《塑料-薄膜和片-样品平均厚度的测量,卷材平均厚度和产量的测量-重量测量法(重量分析厚度)》,方法中主要对取样方法、仪器测试精度、测量压力、测量面积等进行了规定,但是目前没有针对锂电池隔膜制定的标准,实际测试过程中,各家测试条件和实验参数不同,使得测试结果有所出入。
隔膜的克重
锂电池隔膜材料的克重,即面密度,间接反映了同一厚度及原料规格隔膜材料的孔隙率,主要与隔膜原料的密度、隔膜材料的厚度规格有关。锂电池隔膜材料的克重,也影响着锂电池的内阻、倍率、循环性能以及安全性能。表1列举了企业标准中的部分标准。不同类型的锂电池隔膜的克重的检测方法大多数通过电子天平称量若干固定长度和宽度尺寸的试样的质量,计算出对应的克重,取平均值即可。通常会在电子天平上设置输入固定尺寸的试样的克重计算方法,称量后直接显示试样对应的克重读数,计算公式见式(1)。

式中,ρ为克重(面密度),g/m2; m为试样的质量,g; L为试样的长度,m; b 为试样的宽度,m。
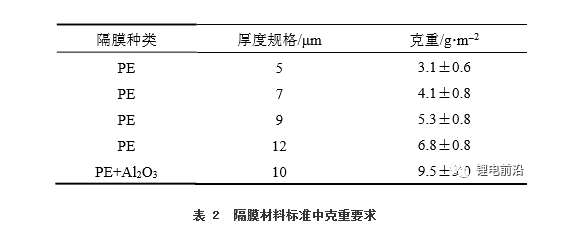
隔膜的微孔结构特征
隔膜的微孔结构特征主要体现在孔隙率和孔径分布两个方面,相对而言孔径分布是评价隔膜品质更重要的指标。孔隙率(p)是孔的体积和隔膜总体积的比值,即单位膜的体积中孔所占体积的百分比,它与原材料树脂以及最终制品的密度有关。膜材料的孔隙,包括通孔、盲孔和闭孔等类型,对于锂离子电池隔膜而言,有用的只有通孔。测定隔膜样品的孔隙率,通常可以采用以下几种方法:电镜观测结合软件处理、称重计算法、液体浸润法以及仪器测定(主要有压汞法、毛细管流动法)。使用扫描电镜可以直观地观测膜表面的成孔状态,然后采用图像处理软件来标记孔径并统计计算孔径分布,大致估算孔隙率。采用此种方法得到的孔隙率比较粗略,不一定能反映隔膜内部的成孔情况。称重法是根据膜材料的密度和膜的表观密度来求孔隙率,见式(2)

式中, ρf为膜的表观密度,采用称重法计算,裁剪一定面积的膜,螺旋测微器测定膜的厚度,得到该膜的体积,称重后计算得
膜的密度。P为膜原材料的密度。该方法需要先测定膜的表观密度,存在着测量误差,而且需要知道膜原材料的密度。液体浸润法是将一定大小的膜干燥称重之后浸入到正丁醇溶液中一定时间后取出,将膜表面的正丁醇采用滤纸轻轻的擦拭掉,称量其重量,然后按照式(3)计算孔隙率

W1为浸润正丁醇之后膜的质量,W2为干膜的质量,V为膜的表观体积,d正丁醇为正丁醇的密度。称重法是求样品质量和没有孔隙的同种材料的质量之比,主要的误差来自对样品体积的计算,同时计算的结果包括闭孔的贡献;通过称量隔膜吸收正丁醇、十六烷等溶剂前后重量的差值,计算出的孔隙率存在较大的随机误差,可大致表征隔膜通孔和盲孔的比例。采用毛细管流动分析仪、压汞仪测定孔隙率,得到的是软件根据孔径分布计算得到的结果,不同仪器测定的结果略有差异。大多数锂离子电池隔膜的孔隙率在35%~ 50%,其中有些商品隔膜(如表面用表面活性剂处理)其孔隙率低于30%,也有的隔膜孔隙率较高,可达60%左右。原则上,对于一定的电解质,具有高孔隙率隔膜可降低电池的阻抗,但孔隙率也并不是越高越好,孔隙率越高,它们的抗力学性能及抗开孔性能变差。即使孔隙率及厚度一致,其阻抗也可能不相同,这是由于孔的贯通性差别所致。孔隙率(p)的计算见式(4)和式(5),一般聚乙烯隔膜理论密度 0.95 g/cm3。
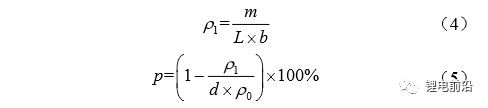
式中,ρ1为试样的面密度,g/m2;m 为试样的质量,g;L为试样的长度,m;b为试样的宽度,m;p为试样的孔隙率,以%表示;d为试样的厚度μm;ρ0为原料的密度,g/cm3。孔径分布可以用毛细管流动分析仪、压汞仪等仪器测定。毛细管流动分析仪通过泡点法测定孔径参数,标准可参考ASTMF316—03。压汞仪测试可参考表1中所列标准。二者测试的结果存在差异,毛细管流动分析仪测试体现通孔的情况,而压汞仪的数据包含盲孔的贡献。
隔膜的力学性能
锂离子电池隔膜的力学性能是隔膜是否易破裂的表征,隔膜破裂会导致电池发生短路,降低成品率,电池的安全性能也会受到影响。隔膜的力学性能主要表现为隔膜的机械强度,一定的机械强度可以保证在电池变形条件下隔膜不发生破裂,降低电池短路风险,提高成品率,提升电池的安全性能,延长电池的使用寿命。机械强度有两个参数,一个是隔膜在长度方向以及垂直方向的拉伸强度及断裂伸长率;另一个是在厚度方向上的穿刺强度。隔膜的拉伸强度是指单位截面的隔膜在拉伸断裂时的拉力,表示隔膜抵抗拉伸的能力,足够的拉伸强度可以防止隔膜变形。与制膜的工艺相关联。采用单向拉伸,膜在拉伸方向上与垂直方向强度不同;而采用双向拉伸时,隔膜在两个方向上一致性会相近。一般拉伸强度主要是指纵向强度要达到100MPa以上。实际的电池制造中,要求的是长度方向的拉伸强度足够高,且横向强度不能太大,过大会导致横向收缩率增大,这种收缩会加大锂电池正、负极接触的概率。断裂伸长率主要是指当隔膜进行断裂拉伸试验时,隔膜样品长度方向增加的百分率,该值主要用来衡量隔膜在未断裂时的延伸能力。隔膜的拉伸强度及断裂伸长率测试采用的标准为《GB/T 1040 3—2006 塑料 拉伸性能的测定 第3部分:薄膜和薄片的试验条件》,涉及到的实验参数主要有夹具距离、拉伸速率、试样尺寸等,目前测试速度50(200、250)mm/min,夹具间距100 mm, 试样尺寸多采用长条型和哑铃型两种,要求测试样品边缘光滑无缺口;一般试验参数不会对结果造成影响,在保证制样质量的情况下,所得结果平行性较好,准确度较高。穿刺强度和电极板表面的粗糙度有关,因隔膜是被夹在凹凸不平的正、负极片间,需要承受很大的压力。为了防止短路,所以隔膜必须具备一定的穿刺强度。电极使用的材料不同,要求隔膜的穿刺强度也不同。如碳素材料颗粒如果细而且没有棱角,要求隔膜的穿刺强度值就比较低,相反,如果颗粒粗而大,并且棱角尖锐,则要求的隔膜穿刺强度就高。足够的穿刺强度可以防止锂枝晶、极片毛刺刺穿隔膜造成短路,穿刺强度值一般在300~ 500gf。但是测试的时候所用的方法和实际电池中的情况有很大的差别,直接比较两种隔膜的穿刺强度不是特别合理。目前,隔膜穿刺强度多采用ASTM D4833— 2007 或 GB/T 10004—2008 要求进行测试,穿刺强度的测试结果与穿刺针的规格、穿刺速率、下夹具的尺寸等有关,目前穿刺针的直径1.0mm,圆球半径0.5mm等较为统一,穿刺速率多采用国标。
隔膜的热收缩及闭孔
聚烯烃隔膜的热收缩与锂电池的安全性能息息相关。一般而言,隔膜的横向(TD方向)对应电池的高度方向。而正极极片宽度+(1~2)mm=负极极片宽度,负极极片宽度+(1~2)mm=隔膜宽度。 烘烤过程中,TD方向的收缩量不能使正负极极片、铝壳接触,即不能超过1~2mm,若超过即会造成正负极短路。 隔膜的纵向(MD 方向)对应电池的宽度方向,即制备工艺的卷绕或叠片方向。卷绕或叠片工艺制备过程中,会将隔膜收紧,胶带黏结。纵向热收缩会使隔膜张紧,极片的横向毛刺会更容易刺穿隔膜,以使电池内部短路。锂电制造商一般会针对不同种类、不同厚度的隔膜在不同温度及时间下的纵向和横向热缩量提出要求(表3为部分举例)。检测方法一般采用《GB/T 12027—2004 塑料、薄膜和薄片加热尺寸变化率实 验方法》。但是对于锂离子电池隔膜,考虑到隔膜在电池极片间的状况,建议参考 UL2591—2009,将隔膜夹在两块钢板之间加固定的压力测试。

锂电隔膜“闭孔”的概念和意义经常被一些产品宣传所滥用并与熔融温度混为一谈。锂离子电池在怎样的异常温度下需要由隔膜闭孔来中止电池的工作?目前在业内还没有形成共识。闭孔测试方法是采用模拟电池测定浸在电解液中隔膜两侧的电阻在温度升高过程中的突变点,参考标准 UL2591—2009。
隔膜的电化学稳定性和抗氧化性
隔膜电化学特性的参数是电化学稳定窗口,主要反映隔膜可以正常充放电的电压上限。电化学窗口可以采用模拟电池做循环伏安测试。但是此测试的结果会受到电解液和添加剂种类的影响。隔膜的抗氧化性主要由材料的基本属性所决定,不因制备方法的不同而改变。不同隔膜抗氧化性的差异将在电池工作一段时间之后逐渐显现,目前没有很好的测试推荐方法。
关于隔膜表面的陶瓷涂覆
随着隔膜的厚度越做越薄,陶瓷涂覆已经成为一种必选的附加工艺。单面涂或者双面涂、对称涂布或者不对称涂布、涂层厚度、涂布层的面密度和颗粒直径、黏结剂和其它添加成分,都是影响涂覆隔膜性能的变量。而涉及涂层的各种因素将对隔膜性能产生非常复杂的影响。但是,这一领域目前还没有相关规范或标准的信息。
隔膜的水分含量
隔膜材料的水分含量主要与隔膜原料的特性及水分含量、车间生产场所水分控制等密切相关。对于目前的锂离子电池隔膜材料行业内关于水分含量的标准要求还没有统一的行业标准,但是随着电动汽车行业的快速发展,特别是动力锂离子电池的品质要求显著提高,锂离子电池隔膜材料的水分含量也将成为衡量隔膜材料质量的重要指标之一。锂电池内部是一个比较复杂的化学体系,这些化学系统的反应结果及过程都与水分密切相关。而水分的失控或粗化控制,导致电池中水分的超标存在,不但能导致电解质锂盐的分解,而且对于正负极材料的成膜和稳定性产生恶劣影响,导致锂离子电池的电化学特性,诸如容量、内阻、产品特性都会产生较为明显的恶化。而隔膜材料的水分含量控制也是控制电池内部含水量的重要环节。
正是因为水分含量比较重要,需要用高灵敏度的卡尔费休方法测试,通常会使用库仑水分仪进行测试:采用I2、SO2、吡啶、无水CH3OH配制成试剂,与样品中水反应,计算出样品中水含量。其测试原理见式(6)和式(7)。

隔膜产品展望
隔膜有多个材料体系,即使是同类隔膜也会因厂家、工艺不同、厚度变化、表面涂布等因素形成不同的系列、规格和质量差异。膜企关注的是隔膜的物理特性,而作为用户的电池制造企业关注的则是隔膜在电池中的应用效果。所以,二者考虑隔膜质量标准的出发点和要求不同。我们需要充分认识到电池制造工艺的复杂性以及影响电池性能因素的复杂性。对于特性型号的电池而言,隔膜材料的选型非常重要。选对适合的材料和规格,是制造出高品质电池的必要条件。随着锂电池产业的迅速发展,业内对隔膜的需求也在不断提高。应合理引导隔膜企业向提高产品质量、规范生产,提升企业国际竞争力的方向发展。